Автоматическое тестовое рентгеноскопическое оборудование в производстве электронных изделий
Общая тенденция к повышению сложности электронной продукции, увеличению количества вводов-выводов применяемых в ней интегральных микросхем при общем уменьшении геометрических размеров и улучшении потребительских свойств самого изделия приводит к стремительному росту количества паяных соединений на печатных платах. Сегодня не редкость платы с 20 тысячами соединений.
Одновременно возрастает и сложность процесса сборки - зачастую в процессе сборочного производства применяются двусторонний поверхностный монтаж, ручная установка компонентов, пайка двойной волной, монтаж прессованием и механическая сборка. И хотя производители стремятся к совершенствованию технологии сборки, очень часто бывает трудно уменьшить количество дефектов на плату, поскольку при возрастании сложности изделия и технологии его изготовления катастрофически увеличивается и количество возможных ошибок.
Поскольку 70-80% всех дефектов являются структурными (производственными), а методы внутрисхемного контроля (ICT) не обеспечивают должного тестового покрытия тестируемого изделия из-за недостаточного доступа к его компонентам, пользователи все более заинтересованы в расширении тестовой стратегии и использовании дополнительно к ICT автоматического тестового оборудования, способного распознавать структурные дефекты на сложных платах. Отметим, что к производственным дефектам относятся обрывы и КЗ, отсутствие или смещение компонента, приподнятые выводы компонентов, некачественная пайка (недопустимое количество пустот в паяном соединении), избыток или недостаток припоя и т.д. При этом ориентация компонентов, а также критерии пайки для выводных, SMT и дискретных компонентов и сборок четко регламентируются международными стандартами IPC A-610C и IPC-7095.
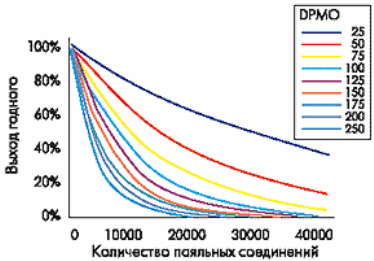 Рис. 1. Соотношение выхода годной продукции и количество паяных соединений на плате. Даже производители мирового класса не в состоянии удерживать выход годных на требуемом уровне для плат с количеством паяных соединений выше 10-15 тыс. (ОРМО - дефектов на миллион возможных)
Время освоения и объем производства
Поскольку жизненный цикл электронного изделия приближается к 1 году, ключевым моментом становится время, необходимое для его освоения. Чем быстрее производители электроники проходят от проекта до опытного образца и затем до его серийного производства, тем выше их доля на рынке, прибыли и доходы. Поэтому необходимы новые тестовые стратегии, сокращающие время разработки тестового ПО и обеспечивающие быстрый и эффективный цикл ввода новой продукции в производство, обеспечивая при этом высокий уровень выявляемости дефектов еще на стадиях разработки продукции. Для освоения новых видов продукции рекомендуются бесконтактные тестовые методы (неэлектрический контроль), такие как автоматический оптический (AOI) и рентгеноскопический контроль (AXI), а также автоматическое тестовое оборудование с подвижными пробниками (FPT), дающие высокий процент обнаружения брака и быстрое внедрение без дополнительных расходов и издержек на контактные устройства (адаптеры).
В выигрыше будут также те компании, которые в состоянии быстро перестроить производство в соответствии со спросом на рынке. В условиях жесткой конкурентной борьбы для этого потребуется надежное распознание дефектов и причин их возникновения, своевременное выполнение корректирующих и предупреждающих воздействий.
Таблица 1. Тестовое покрытие различных методов тестирования
|
FT |
ICT |
MDA |
FPT |
AXI |
AOI |
API |
HVI |
КЗ |
2 |
1 |
2 |
1 |
2 |
2 |
2 |
2 |
Обрывы |
3 |
3 |
2 |
1 |
2 |
2 |
2 |
2 |
Непропай |
3 |
2 |
3 |
1 |
3 |
3 |
3 |
3 |
Не тот компонент |
3 |
3 |
1 |
3 |
1 |
1 |
1 |
2 |
Негодный компонент |
3 |
3 |
3 |
3 |
2 |
2 |
1 |
1 |
Пропущенный компонент |
1 |
3 |
1 |
1 |
1 |
1 |
1 |
2 |
Неверная ориентация |
2 |
3 |
1 |
2 |
1 |
1 |
1 |
2 |
Функциональные ошибки |
3 |
3 |
3 |
3 |
3 |
3 |
3 |
2 |
Сокращения:
- HVI - неавтоматический визуальный контроль,
- API - автоматический контроль нанесения паяльной пасты,
- AOI - автоматический оптический контроль,
- AXI - автоматический рентгеноскопический контроль,
- FPT - тестирование с помощью подвижных пробников,
- MDA - анализ производственных дефектов,
- ICT - внутрисхемное тестирование,
- FT - функциональное тестирование.
Обозначения:
- 3 - плохо, 2 - хорошо, 1 - очень хорошо.
Никакая в отдельности взятая методика тестирования не решает всех проблем. У каждой есть свои плюсы и минусы, и каждая методика должна оцениваться как потенциальное решение в рамках общего плана тестирования. Хотя методы автоматической инспекции позволяют обнаружить дефекты на более ранних стадиях, быстро отладить и отремонтировать изделие, они не дают такой уверенности в функционировании продукции, как, например, внутрисхемные или функциональные методы. Оптимальную тестовую стратегию чаще всего обеспечивает комбинированный подход (распределенное тестирование), обеспечивающий баланс между такими требованиями как тестовое покрытие, выявляемость дефектов, доступ, время внедрения тестирования, время безотказной работы, общая экономия средств и производительность.
Контрактное производство
Постоянный рост доли контрактных производителей на рынке также способствует развитию автоматических методов контроля, таких как AXI. Причина в том, что OEM-производители возлагают ответственность за сборочные дефекты на своих субподрядчиков - контрактных производителей, и обеим сторонам нужны тестовые технологии, которые позволят определить ответственность за структурные дефекты.
Некоторые виды изделий, особенно сложные, часто ожидают некоторое время своей очереди на отладку и настройку у квалифицированных отладчиков, которых не хватает, тем более что у контрактных производителей появилась тенденция использовать временную рабочую силу.
Таким образом, производители должны найти тестовые решения, которые позволят преодолеть проблему нехватки квалифицированных кадров и обеспечить непрерывное производство. Тестовые методы AXI помогут в этом, обеспечив легкоприменимые решения, сокращающие время обучения операторов за счет превращения задач по разработке и отладке в определение доступности паяных соединений.
Таблица 2. Уровни тестового доступа при использовании 2D AXI на двусторонних платах
|
Размеры платы (мм) |
Количество компонентов |
Количество соединений |
Доступ к компонентам |
Доступ к соединениям |
Плата 1 |
419x190 |
1664 |
8869 |
95% |
67% |
Плата 2 |
305x254 |
1503 |
12945 |
86% |
83% |
Плата 3 |
355x280 |
963 |
6753 |
69% |
58% |
Таблица 3. Уровни тестового доступа при использовании 2D AXI при двухпроходном тестировании на двусторонних платах
|
Доступ при первом проходе |
Доступ при втором проходе |
Общий тестовый доступ |
Компоненты |
Соединения |
Компоненты |
Соединения |
Компоненты |
Соединения |
Плата 1 |
62% |
44% |
36% |
39% |
98% |
83% |
Плата 2 |
71% |
29% |
23% |
62% |
94% |
91% |
Плата 3 |
44% |
38% |
31% |
34% |
75% |
72% |
Тестовый доступ
Просвечивающий автоматический рентгеноскопический контроль (AXI)
Рентгеноскопический контроль или 2D AXI состоит из источника рентгеновских лучей и приемника, между которыми под углом 90° к рентгеновскому излучению помещается испытываемое изделие.
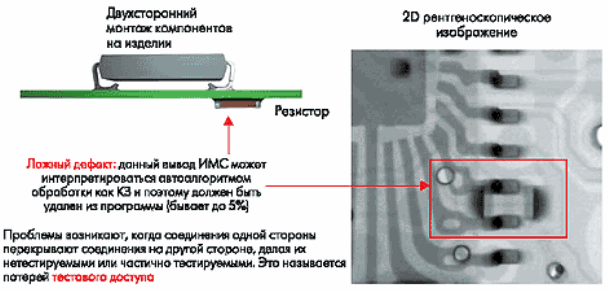 Рис. 2. При 2D AXI паяные соединения на одной стороне платы могут закрывать видимость соединений на другой стороне, уменьшая тестовый доступ
Паяные соединения на обеих сторонах тестируемого изделия отображаются одновременно, и обычно они достаточно хорошо отличимы друг от друга. Проблемы возникают в тех случаях, когда паяные соединения одной стороны тестируемого изделия перекрывают соединения на другой стороне, делая их нетестируемыми или частично тестируемыми. Это называется потерей тестового доступа. В таком случае некоторые компоненты на испытываемом изделии могут быть недоступными для тестирования.
В таблице 3 показано, как улучшается доступ при тестировании двусторонних плат в два этапа: один после сборки на нижней стороне, другой - после сборки на верхней стороне, поскольку, хотя доступ на втором этапе остается таким же, как при тесте в один этап, доступными являются почти 100% паяных соединений первого этапа. Хотя подобная методика повышает накладные расходы за счет введения второй стадии тестирования, во многих случаях она позволяет повысить скорость обратной связи с производственной линией и имеет преимущества по сравнению с 3D-технологией, о чем будет сказано позже.
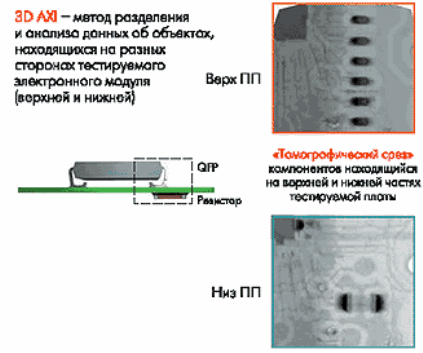 Рис. 3. При 3D AXI используется цифровой томосинтез или технологии ламинографии
Применение цифрового томосинтеза или методов ламинографии, то есть трехмерного автоматического рентгеноскопического контроля (AXI) позволяет получать независимое друг от друга одновременное отображение двух сторон платы. При этом исчезают проблемы наложения паяных соединений, хотя наличие теневых эффектов не позволяет ламинографическим системам достигнуть тестового покрытия 100%. Цифровой томосинтез в принципе дает больший доступ, чем ламинография, вследствие способности полностью снимать эффекты затемнения от устройств на противоположной стороне платы.
Требуемые уровни тестового доступа
Нужно ли тестировать каждую двустороннюю плату с максимально возможным доступом? Многолетний производственный опыт дает отрицательный ответ на этот вопрос. Производители электроники вложили миллионы долларов и использовали опыт и знания, накопленные десятилетиями, для создания производственных групп, технологий и оборудования, создающих продукты высокого качества и надежности, и эти технологии не требуют 100-процентной проверки, что является относительно новой идеей для этого сектора.
Поэтому, вероятно, 3D AXI требуется не для каждой отдельно взятой платы.
Каждая стадия тестирования в производственном сборочном процессе служит двум большим задачам:
- распознать и не пропустить дальше дефекты, допущенные на предыдущих стадиях;
- обеспечить обратную связь и обработать данные тестирования для генерации корректирующих и предупреждающих воздействий.
Давайте рассмотрим эти цели в контексте использования AXI.
Ни один метод тестирования никогда не обеспечит 100-процентного обнаружения дефектов и тестового доступа. Достоинства метода тестирования определяются способностью обеспечить оптимальный баланс между производительностью, тестовым покрытием, общей экономией расходов, расходами на сервисную поддержку, временем освоения нового изделия, продолжительностью безотказной работы и множеством прочих факторов, специфических для каждого отдельного производителя. Неправильно было бы предположить, что оптимальный баланс этих факторов наблюдается просто в момент достижения максимального тестового доступа.
Конечно, в некоторых случаях тестовый доступ AXI должен быть максимальным, но даже подобные случаи требуют внимательного рассмотрения в контексте распределенной тестовой стратегии, при которой разные методы тестирования применяются для комплементарного и избыточного тестирования. Паяные соединения, которые невозможно протестировать с помощью AXI, могут быть протестированы позднее с помощью ICT (например, методами OpenFix - с помощью комплекта емкостных пробников).
Таким образом, использование дополнительных тестовых стратегий может смягчить потери доступа на одной тестовой стадии с минимальным воздействием на качество продукции и эффективность производства, а специализированное программное обеспечение, предназначенное для проектирования процесса тестирования - DfT (design-for test) может ещё более упростить и автоматизировать распределение тестов.
Что же касается обратной связи данных измерений процесса сборки, большая часть усилий специалистов концентрируется на анализе распределений дефектов по платам, по времени, по стадиям техпроцесса, по компонентам и т. д. Такой тип анализа основан на статистическом принципе, который гласит, что получение соответствующих тестовых данных вполне достаточно для того, чтобы выявить любые причины отклонений, присущих производственному процессу.
Ограничение доступа при внутрисхемном тестировании (ICT)
Многие производители электроники применяют тестовые методы AXI как дополнение к тестовым возможностям ICT, которые все более ограничиваются в связи с растущей тенденцией уменьшения физического доступа к контактным площадкам тестируемого изделия. Обе стратегии AXI (в этом плане эффективнее 3D AXI) могут существенно уменьшить количество подпружиненных контактов (пинов), необходимых для реализации ICT, и, тем самым, оптимизировать дополнительное пространство на тестируемом изделии, необходимое для размещения на нем контактных тестовых площадок. Распределение тестирования между ICT и AXI, а также уменьшение общего количества тестовых пинов упрощаются при использовании программного обеспечения DfT.
Сравнение AXI-технологий
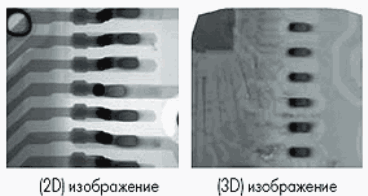 Рис. 4. Качество изображения 2D лучше чем 3D
Мы рассмотрели вопросы по уровню доступа для методов 2D и 3D AXI. Давайте остановимся на некоторых различиях, влияющих на эффективность этих технологий в промышленных условиях.
Любой автоматический контроль основан на базовых принципах обработки изображения. В данном случае имеются различия в способах трансляции тестовых программ, выявляемости дефектов, производительности систем, затрат на их обслуживание и сроках окупаемости.
Пользователи должны понимать природу этих различий и соизмерять их эффект в сочетании с тестовым доступом при определении оптимальной тестовой AXI-стратегии.
Контраст изображения
Автоматическая система контроля определяется качеством изображения - чем выше качество, тем лучше контроль. Для обеих AXI-методик алгоритмы обработки изображения и распознавания дефектов основываются на измерении геометрических размеров и анализе галтелей паянных соединений по градациям оттенков серого. Для этого, в свою очередь, требуется, чтобы контраст изображения, то есть разность яркости между исследуемым местом (паяное соединение) и окружающей зоной, был как можно выше.
При 2D AXI рентгеновское излучение проходит через плату под углом 90°, в то время как при 3D AXI для получения изображения используется вращение приемника (ламинография) или просвечивание под углом (цифровой томосинтез). Это означает, что 2D AXI обеспечивает больший контраст изображения и резкость очертаний, чем 3D, а, следовательно, дает лучшее распознавание дефектов, повторяемость замеров и достоверность.
Выявляемость дефектов
Оба метода обеспечивают примерно одинаковый уровень выявляемости дефектов для большинства дефектов пайки, включая дефекты BGA, хотя 2D AXI благодаря лучшему контрасту изображения позволяет идентифицировать мелкие и труднораспознаваемые дефекты пайки (такие как непропай), а способность распознавать более мелкие объекты и границы паяных соединений позволяет распознавать дефекты пайки BGA. Хочется сказать особо об одном чрезвычайно важном положении, которое, кстати, может служить косвенным свидетельством качества программного обеспечения рентгеноскопических систем. Заключается данное положение в том, что именно программное обеспечение должно принимать окончательное решение об исправности тестируемого изделия. Поясняет данное положение рис. 5. При внимательном изучении этого рисунка становится понятно, что даже имея рентгеноскопическое изображение BGA, оператор не может принять корректное решение о годности пайки его шариков без программно выполняемого автоматического анализа. Заметим, что такой анализ имеют и могут качественно выполнять далеко не все рентгеноскопические системы.
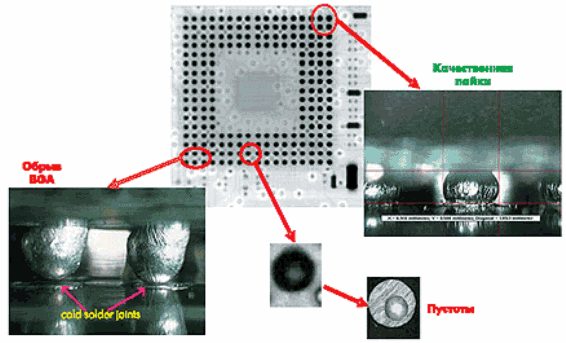 Рис. 5. Рентгеноскопические системы фирм TERADYNE и VISCOM автоматически принимают решение о годности изделия
Таблица 4. Сравнительная таблица выявляемости дефектов при 2D и 3D тестировании
|
Тип дефекта |
2D AXI |
3D AXI |
Любые корпуса ИМС |
Объемный (вне рентгеноскопического среза) |
1 |
3 |
QFP |
Неприпаянные или поднятые выводы |
1 |
1 |
Недостаток припоя |
1 |
1 |
КЗ |
1 |
1 |
Пластиковые BGA |
Неприпаянные или поднятые выводы |
2 |
1 |
Недостаток припоя |
3 |
3 |
КЗ |
1 |
1 |
Раковины в припое |
1 |
2 |
Керамические BGA |
Неприпаянные или поднятые выводы |
3 |
2 |
Недостаток припоя |
2 |
2 |
КЗ |
1 |
1 |
Разъемы, монтируемые в отверстия |
Недостаток припоя |
3 |
1 |
КЗ |
1 |
1 |
Соединения обжимкой |
Изогнутые выводы |
1 |
3 |
Обозначения:
- 3 - плохо, 2 - хорошо, 1 - очень хорошо.
Сравнение технологий 2D и 3D AXI по производительности
Поскольку качество изображения выше при 2D AXI, этот метод дает более широкий оперативный простор производителям, которые могут инспектировать платы при меньшем увеличении, получать больший охват площади платы рентгеновским изображением, тем самым повышая общую производительность тестирования.
3D-ламинография использует технологию "лазерной топографии поверхности" для определения топологии поверхности платы с целью точного задания положения ламинографического среза. Данная технология не только менее производительна, чем 2D AXI, но и отрицательно влияет на способность качественного ламинографического контроля при малых увеличениях.
Коробление и дрожание плат также создает проблемы при 3D-ламинографии, поскольку значительное количество паяных соединений в связи с тенденцией к их катастрофической миниатюризации может оказаться вне фокуса, и не поддаваться контролю или доступу вообще. Все это уменьшает тестовое покрытие, приводит к появлению ложных дефектов, увеличивает время настройки тестовой системы и требует частого вмешательства в тестовую программу. Также являясь 3D-технологией, цифровой томосинтез лишен этих недостатков, так как использует метод цифрового синтезирования образа исследуемого объекта. Цифровой томосинтез можно назвать гибридной технологией, объединяющей достоинства 2D и 3D-технологий.
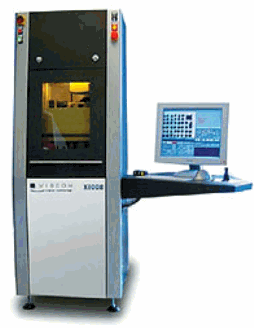 Рис. 6. Автоматическая регнтгеноскопическая 2D-система X8006-12 фирмы VISCOM
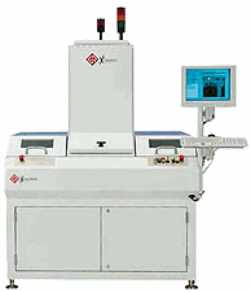 Рис. 7. Комбинированная автоматическая регнтгеноскопическая 2D/3D-система XSTATIONS HS фирмы TERADYNE
Заключение
Каждый потенциальный пользователь AXI должен внимательно оценить окупаемость, простоту использования, тестовое покрытие и другие характеристики выбранной тестовой стратегии. Исходя из упрощенного подхода системы 2D AXI примерно на $100-150 тыс. дешевле, чем 3D, однако стоимость оборудования - это только часть общей картины. Возврат капиталовложений для любой тестовой стратегии зависит от множества факторов, таких как время безотказной работы, механические характеристики тестовой системы, время разработки, отладки и оптимизации тестового ПО, повторяемость результатов, тестовое покрытия. Кроме того, необходимо учитывать стоимость и качество технической поддержки оборудования.
В заключение отметим, что в последнее время на российском рынке появилась возможность реализации заказного (контрактного) тестирования, в том числе тестирования на автоматических рентгеноскопических установках X-Ray, что позволяет выпускать с высоким качеством сложную электронную продукцию любой серийности.
Игорь Рыков
|