Школа схемотехнического проектирования
устройств обработки сигналов
Занятие 15. Практические рекомендации по разработке печатных плат
- Никогда не рисуйте то, что можно скопировать.
- Никогда не копируйте то, что можно обвести.
- Никогда не обводите то, что можно вырезать и наклеить.
Закон Мерфи
Современные электронные узлы значительно отличаются от устройств разработки конца 80-х — начала 90-х годов прошлого века. Во-первых, новые технологии поверхностного монтажа привели к уменьшению габаритов компонентов в 3–6 раз. Во-вторых, появились новые корпуса интегральных схем с малым шагом между выводами (0,5–0,65 мм), корпуса с шариковыми выводами (BGA), новые малогабаритные дискретные компоненты и соединители. В-третьих, повысилась точность изготовления печатных плат, увеличились возможности для разводки сложных устройств в малых габаритах. Появление новой элементной базы позволяет говорить о возможности воплощения сложных систем на одной плате и даже на одном кристалле (system-on-chip). Это означает, что на одной и той же типичной плате устройства обработки сигналов в малых габаритах размещаются высокочувствительный аналоговый тракт, аналого-цифровой преобразователь, высокоскоростная схема цифровой обработки на процессоре и (или) программируемых логических интегральных схемах, буферные элементы и драйверы линий связи, элементы стабилизаторов напряжения питания и преобразователей уровня, а также другие узлы. Естественно, это накладывает отпечаток на методологию разработки платы.
Сближение ролей разработчика и конструктора в современном процессе проектирования изделия и побудило меня включить занятие по печатным платам в цикл статей по схемотехническому проектированию [3]. Естественно, более полную информацию можно получить других в работах [1, 2]. Как известно, печатная плата представляет собой изоляционное основание с нанесенными на него тонкими электропроводящими покрытиями, которые выполняют функции монтажных проводов и элементов схемы (например, конденсаторов, катушек индуктивности, переключателей, электрических разъемов и т. д.). ПП является деталью, так как она не требует при изготовлении сборочных операций.
Идея изготовления ПП была предложена и запатентована в 1940 году в Англии П. Айслером. На металлизированную поверхность платы Айслер наносил (аналогично принципу клише) кислотостойкой
краской нужный рисунок проводников. Затем травлением в кислоте удалялся незащищенный слой фольги, после чего щелочью удалялась краска и образовывалась топология разводки.
Современное электронное устройство невозможно представить без применения технологии поверхностного монтажа. Преимущества поверхностного монтажа неоспоримы — высокая плотность компоновки, улучшение электромагнитной совместимости; таким образом, даже в опытных разработках будущее за поверхностным монтажом.
Первые корпуса для поверхностного монтажа появились в конце 50-х — начале 60-х годов прошлого века. Корпуса типа flat pack представляли собой металлический корпус с двусторонним расположением выводов. Отечественному разработчику такие корпуса известны как корпуса «типа 4», в которых было выпущено огромное количество ИС для применений в специальной технике.
Ныне применяется огромное число корпусов поверхностного монтажа с шагом между выводами до 0,5 мм и массивами шариковых выводов (BGA). Некоторые особенности имеет технологический процесс монтажа печатных плат с применением SMD-компонентов.
При использовании поверхностного монтажа дискретные компоненты и микросхемы с шагом выводов более 1 мм должны быть размещены так, чтобы выводы компонентов не выходили за пределы контактной площадки (рис. 1). Оптимально симметричное расположение компонентов. Такие компоненты паяются методом групповой пайки в конвекционных печах.
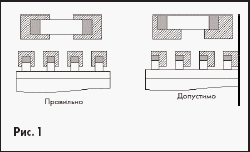
Современные микросхемы имеют, как правило, шаг выводов 0,5–0,8 мм и большое количество выводов на 2 или 4 стороны. При ручной установке их на плату для вспомогательной фиксации компонентов используется специальная мастика. Выводы паяются при помощи фломастера с флюсом и наконечника «микроволна» паяльной станции. При пайке групповым методом требуется применение тонкого наконечника (0,3 мм) для диспенсера.
В связи с преимущественным использованием поверхностного монтажа обычные компоненты применяются из-за большой рассеиваемой мощности и в высоковольтных цепях для обеспечения достаточного изоляционного зазора. В большинстве случаев в качестве дополнительного теплоотвода используются широкие проводники платы, поэтому при монтаже важную роль играет сокращение длины выводов компонентов для уменьшения теплового сопротивления. Также в большинстве случаев следует стремиться к обеспечению минимальной высоты монтажа. Массивные и крупные компоненты (электролитические конденсаторы, трансформаторы и т. д.) монтируют вплотную к плате для увеличения стойкости к ударам и вибрации. Компоненты в DIP-корпусах необходимо монтировать как можно ближе к плате, чтобы их выводы были как можно короче для обеспечения минимального теплового сопротивления (рис. 2).
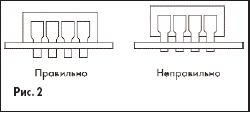
Компоненты с аксиальными выводами монтируются, как правило, вертикально для лучшего воздушного охлаждения. При этом диоды и стабилитроны следует устанавливать катодом (цветной полосой) вверх с зазором 1–2 мм между корпусом прибора и платой. При достаточном месте для размещения их располагают горизонтально. В этом случае между такими компонентами и платой следует оставить воздушный зазор или установить прокладку 1–2 мм (рис. 3).
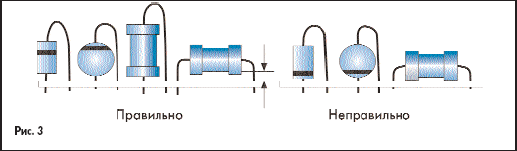
Компоненты с выводами в одну сторону — керамические и пленочные конденсаторы, резонаторы, варисторы, полупроводниковые предохранители — монтируются из условия обеспечения минимального зазора (примерно 1 мм) между корпусом компонента и платой и отсутствия механических напряжений выводов.
Литиевые источники питания имеют очень большую чувствительность к токам разряда. Платы с установленными литиевыми элементами нельзя мыть с использованием токопроводящих растворов, поэтому их следует монтировать в последнюю очередь, после всех промывок.
Кварцы в низких корпусах следует устанавливать с минимальным зазором к печатной плате. Если под кварцем нет переходных отверстий и токопроводящих проводников, то рекомендуется установка вплотную к плате. Кварцы в высоких корпусах H49 и часовые кварцы следует укладывать на печатную плату в свободную сторону или на земляной проводник. По возможности корпус кварца следует фиксировать каплей припоя к земляному проводнику.
Светодиоды в удлиненных корпусах диаметром 5 мм следует монтировать вплотную к плате, светодиоды в миниатюрных корпусах 3 мм впаиваются по фиксирующие выступы на выводах (рис. 4).
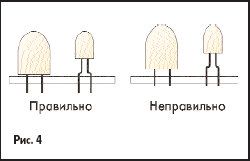
Электролитические конденсаторы со штыревыми выводами используются в мощных высокочастотных преобразователях и высоковольтных (более 50 В) цепях. Эти конденсаторы имеют модернизированный корпус с газовыделительным клапаном и картонной или резиновой установочной прокладкой и рассчитаны на монтаж вплотную к плате.
Обычно на корпусе маркируется отрицательный (минус) вывод конденсатора. Иногда для снижения общей высоты монтажа их укладывают на плату (рис. 5).
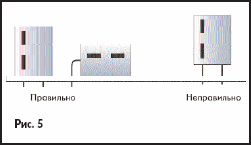
Механические компоненты — кнопки, разъемы, джамперы, ЖКИ, клеммники — обычно имеют механические привязки к нескольким элементам конструкции — платам или элементам корпуса. Точность их размещения задается конструктором по точкам привязки на плате. Если нет конструкторских требований по установке данного компонента, то необходимо монтировать компонент по монтажным точкам, без перекосов и зазоров. В этом случае заботы о правильном размещении компонента остаются за конструктором.
Все полярные компоненты следует размещать одинаково ориентированными. Компоненты должны устанавливаться не ближе чем 0,2 дюйма к краю платы. Следует обратить внимание на электроизоляцию отверстий механического монтажа. В слое металлизации нужно избегать «внутренних» острых углов. Проводящие дорожки должны быть не ближе 20 mil от края платы.
С точки зрения монтажа не существует максимального рекомендуемого расстояния между компонентами — чем больше, тем лучше, в пределах разумного конечно. Однако некоторые проекты требуют как можно более плотного размещения компонентов на плате. Пример минимальных рекомендуемых расстояний при компоновке платы представлен на рисунке 6.
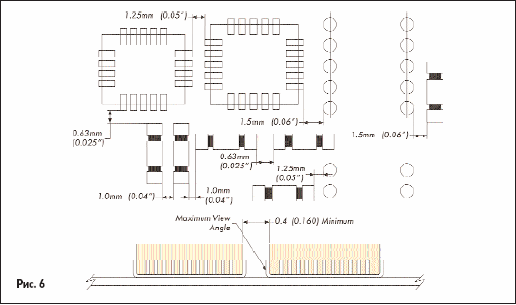
Расстояние между компонентом и краем платы должно быть не менее 1,25 мм (50 mil). Все полярные планарные компоненты должны быть по возможности сориентированы в одном направлении. При проектировании плат следует учитывать предпочтительное расположение компонентов. Все пассивные компоненты должны быть расположены параллельно друг другу, все компоненты в корпусах SOIC должны размещаться перпендикулярно длинной оси пассивных компонентов, при этом длинная ось SOIC должна быть параллельна направлению движения платы при пайке «волной». Компоненты одного типа предпочтительно размещать в одном направлении и по возможности группировать их вместе.
Для проектов, использующих традиционные компоненты, рекомендуется сетка размещения 2,5 мм (100 mil), для более плотного размещения при использовании SMT-разработок сетку размещения можно уменьшить до 0,63 мм (25 mil). Следует различать двусторонний и односторонний монтаж компонентов. Разработчики должны стараться разместить все компоненты на одной стороне (primary side) платы. В противном случае это повлечет за собой удорожание платы.
Метка точки отсчета (fiducial marks) является центром системы координат на всех этапах производства платы и монтажа. Она позволяет оборудованию корректировать погрешности измерения текущих координат, накапливающиеся в процессе монтажа. Существует два вида меток начала отсчета: глобальные и локальные. Первые используются для всей платы или — в случае, если несколько плат объединены в панель, — для привязки всей панели. Вторые используются для привязки конкретного компонента (обычно с большим количеством ножек и маленьким шагом между ними). Для корректного вычисления координат (X, Y offsets)
требуются минимум две глобальных метки, обычно расположенные в диагонально-противоположных углах платы, на максимально возможном друг от друга расстоянии.
Для корректного вычисления координат некоторых компонентов также требуются две локальные точки отсчета, расположенные обычно по диагонали, на периметре области, занимаемой данным компонентом. В случае нехватки свободного места разрешается использовать одну локальную точку отсчета, предпочтительно в центре занимаемой компонентом области. Рекомендуемый размер метки — 1,5 мм (60 mil) и для глобальных, и для локальных меток. Иногда используют глобальные метки большего размера, чем локальные. Минимальный размер метки — 1,0 мм (40 mil), максимальный — 3,0 мм (120 mil). Между меткой и остальными частями платы должен быть зазор (рис. 7).
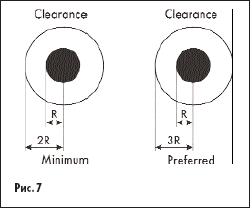
Метка должна быть изображена в слое металлизации, освобождена от маски и покрыта сверху никелем или оловом. Между метками и краем платы должно быть расстояние не менее 5 мм (200 mil) плюс минимальный требуемый зазор (2R). Координаты первой точки — (0, 0), две остальные метки расположены на осях X и Y. Глобальные метки начала отсчета должны располагаться на всех слоях, содержащих компоненты.
Использование поверхностного монтажа существенно увеличивает плотность установки компонентов на плату. В современных производствах поддерживается ширина проводника и зазора 0,15 мм (6 mil) (5-й класс точности платы), которая на сегодняшний день наиболее распространена и в основном заменила величину 0,3 мм (12 mil). Часто применяют ширину проводника и зазора 0,125 мм (5 mil).
Широкие проводники, подходящие к контактным площадкам, могут помешать хорошему припаиванию элементов, так как тепло будет «уходить» с площадки по широкому проводнику, в результате пайка получится «холодной». Варианты решения проблемы:
- Используются узкие проводники, соединяющие непосредственно контактную площадку и широкий проводник, как показано на рис. 8. Ширина подводящего, «узкого», проводника может варьироваться в пределах 0,25–0,125 мм;
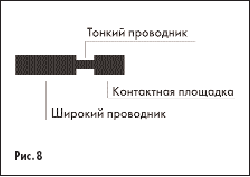
- Проводить дорожки между соседними площадками рекомендуется так, как показано на рис. 9, при условии отсутствия жестких требований к длине проводника;
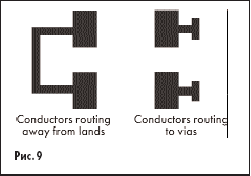
- Со всех сторон контактной площадки наносят маску, которая препятствует перемещению расплавленного припоя вдоль проводника. Этот способ может успешно применяться, когда игнорируются первые два.
Рекомендуемый размер площадки под переходное отверстие при 4–5-м классе точности платы должен быть равен диаметру отверстия плюс 0,4–0,5 мм. Размер переходных отверстий должен выбираться в зависимости от толщины платы и рекомендованного производителем отношения толщины платы и минимального диаметра металлизированного отверстия.
Монтаж элементов можно производить как на отдельной плате, так и на нескольких платах, объединенных в панель. Платы или панели, которые должны подвергаться автоматическому монтажу, имеют некоторые особенности.
Обычно на краях панели (платы) оставляют свободную с двух сторон от компонентов полоску шириной от 3,8 (150 mil) до 10 мм (400 mil). В каждом случае ширина полоски зависит от требований конкретного производителя (мы рекомендуем 10 мм).
При групповой пайке SMD-компонентов необходимо визуально проверить платы на отсутствие обрывов и перемычек. Контроль должен быть проведен максимально тщательно, это сэкономит множество усилий по выявлению ошибок на следующих стадиях.
Перед пайкой необходимо промыть заготовки печатных плат для устранения следов загрязнений, обезжиривания и активизации поверхности. Промывать можно спиртом или смесью, затем нанести на площадки предварительно подготовленную для обеспечения необходимой вязкости припойную пасту. Нанесение возможно при помощи диспенсера (дозатора) или трафаретным способом. Далее производится установка компонентов в соответствии с представленной документацией.
Необходимо соблюдать температурный профиль пайки. Существует стандартный температурный режим (рис. 10), подходящий для большинства компонентов и паяльных паст, и отдельные его участки важны для обеспечения конечного качества.
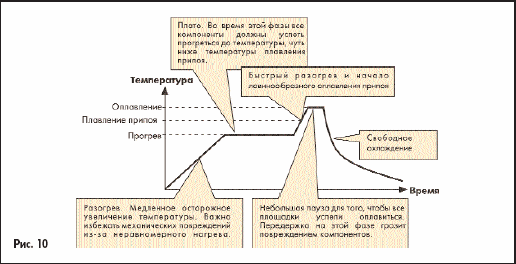
Мы рассмотрели некоторые особенности проектирования и производства современных печатных плат. Безусловно, правильное понимание схемотехником значения конструкции позволит получить быстрый и качественный результат.
Литература
- Стешенко В. Б. ACCEL EDA: технология проектирования печатных плат. — М.: «Нолидж». 2000.
- Стешенко В. Б. ПЛИС фирмы ALTERA: проектирование устройств обработки сигналов. М: «Додэка». 2000.
- Стешенко В. Б. Школа схемотехнического проектирования устройств обработки сигналов // Компоненты и технологии. 2000. No 3–8; 2001. No 1–7; 2002. No 1.
Владимир Стешенко
|